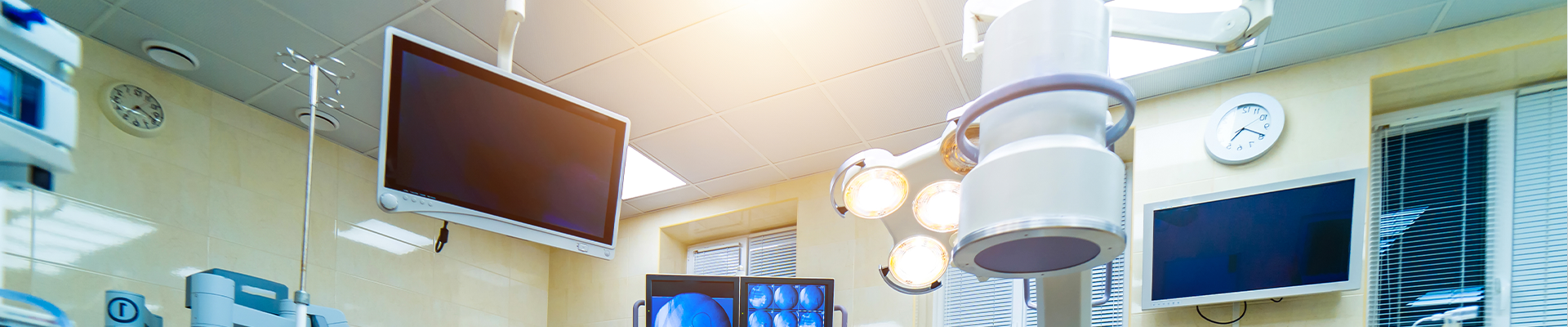
Engenharia Clínica
A OPUS MEDICAL destaca-se na gestão integral do parque e dos processos de equipamentos, alinhando-se às normativas da Anvisa. Seu serviço de Engenharia Clínica busca a acreditação hospitalar conforme as diretrizes da Organização Nacional de Acreditação (ONA) e ISO 9001.
A expertise acumulada pela OPUS MEDICAL na área de Engenharia Clínica representa um substancial apoio para os hospitais que almejam a acreditação nos níveis 1, 2 e 3. A empresa conta com uma equipe composta por técnicos qualificados, engenheiros e gestores da qualidade, aptos a conduzir todas as fases do processo de acreditação, especialmente no que concerne à manutenção de equipamentos médico-hospitalares.
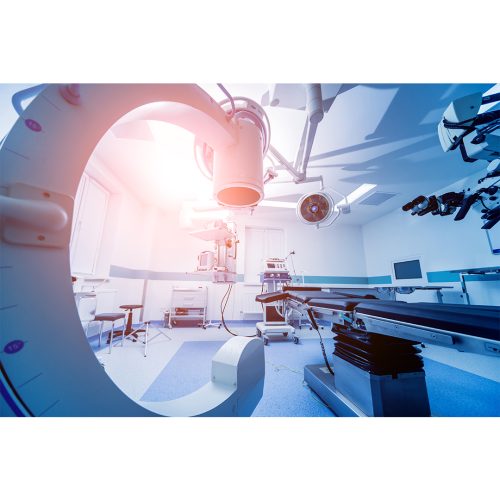
Através de nosso departamento de Engenharia Clínica, auxiliamos na avaliação para aquisição de equipamentos, peças e acessórios, fazendo o estudo da viabilidade de incorporações tecnológicas, custo pós manutenção/custo preventiva/corretiva. Além disso, fazemos a gestão de todos os equipamentos médico-hospitalares, incluindo o gerenciamento da equipe técnica, controlando o ciclo de vida dos equipamentos através de registros, relatórios e levantamentos estatísticos, assim como levantamento de custos operacionais.
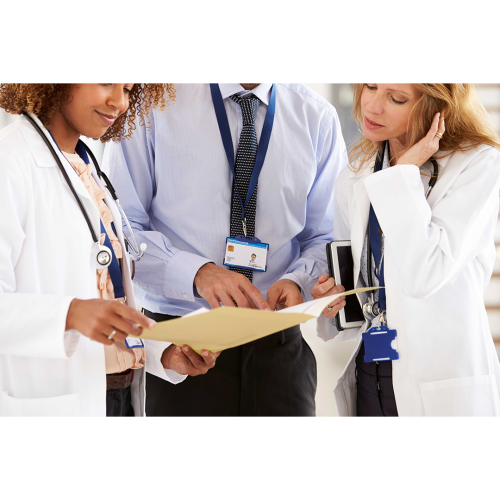
Realizamos a calibração de equipamentos médico-hospitalares como parte essencial dos cuidados técnicos aplicados para garantir o funcionamento regular e permanente desses aparelhos. Este processo inclui inspeções periódicas, substituição de componentes e a adoção de práticas que visam manter as condições de uso em níveis desejáveis de segurança, seguindo as normas técnicas estabelecidas pela Anvisa e/ou as recomendações dos fabricantes.
Além disso, executamos operações destinadas a corrigir qualquer defeito nos equipamentos, com a substituição de componentes, agindo de maneira a reparar os problemas no menor tempo possível. Essas ações visam favorecer o bom andamento das atividades da instituição, contribuindo para o conforto e bem-estar tanto dos pacientes quanto dos funcionários.
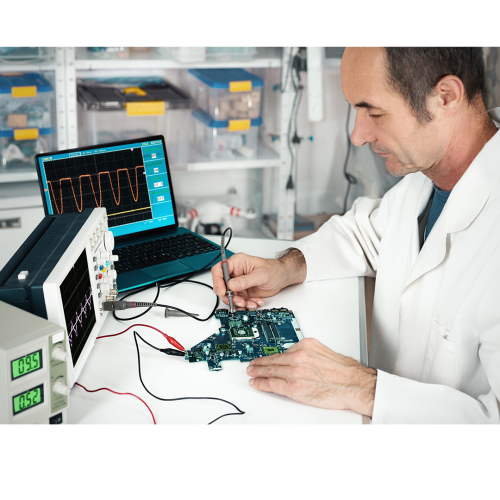
Em trabalho conjunto com a equipe de enfermagem, o plano de educação continuada em equipamentos médicos auxilia na melhora acentuada no aproveitamento das máquinas tanto em exploração dos recursos tecnológicos adicionais dos equipamentos quanto em relação ao cuidado com a operação dos mesmos.
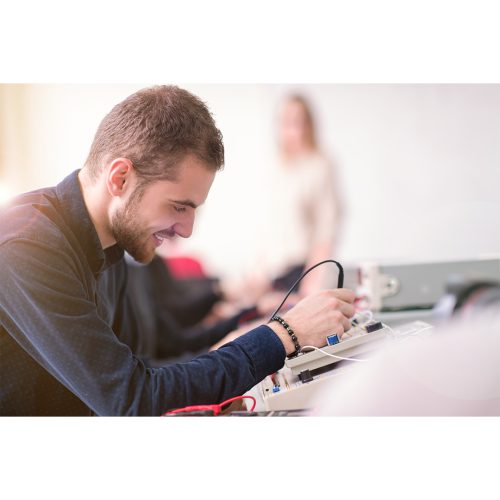
Disponibilizamos para nossos clientes Software de gestão de Engenharia Clínica:
O software possui banco de dados relacional, transacional e WEB, permitindo níveis de segurança e acesso diferenciado por senhas, possibilitando o acesso da Gerência Hospitalar às informações do setor.
O sistema permite o cadastro de equipamentos por tipo, facilitando a análise das quantidades, normas técnicas pertinentes, dados de fabricantes e fornecedores, além de controlar garantias e manutenções preventivas, elaboração de relatórios técnicos que poderão estar associados às Ordens de Serviço ou a um determinado tipo de equipamento.
A ferramenta permite avaliação do Setor de Engenharia Clínica e seus profissionais através de indicadores de desempenho, contemplando os Relatórios de Produtividade como:
- Tempo Médio entre Falhas
- Tempo Médio de Atendimento
- Tempo Médio de Solução
- Índice de Rechamada por equipamento
- Produtividade por Técnico
- Produtividade por Setor
- Ordens de Serviço por setor (ou centro de custos)
- Ordens de Serviço por período
- Ordens de Serviço por equipamento
- Ordens de Serviço por técnico
- Ordens de Serviço pendentes
- Ordens de Serviço encerradas
- Custo de manutenção por equipamento
- Custo da hora técnica por técnico
- Custo médio de manutenção do equipamento
- Custo de manutenção por período
- Custo total de manutenção por período
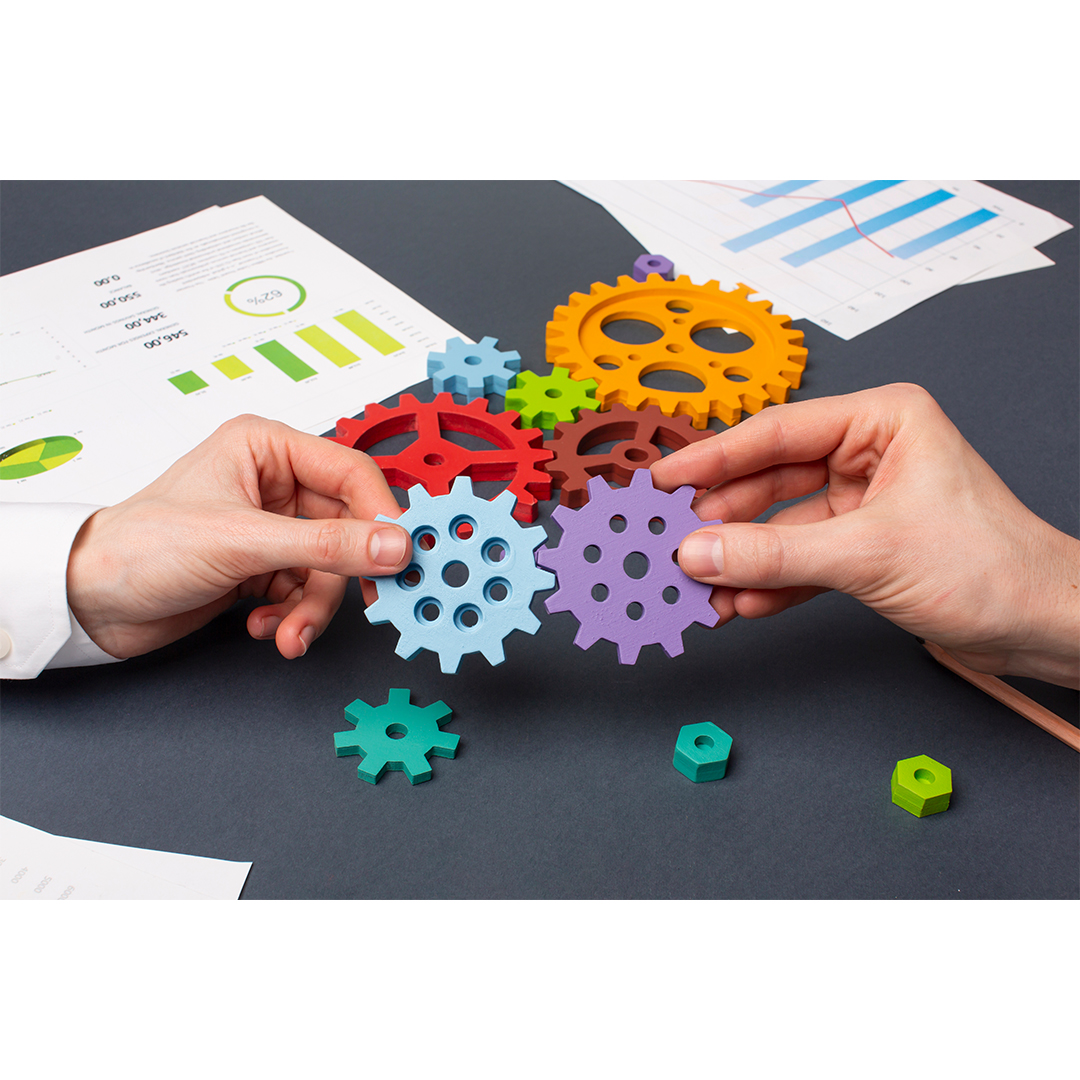
Dentro dos procedimentos de Engenharia Clinica fazemos o gerenciamento de risco que é importante para a segurança direta do paciente, usuário e da instituição.
No uso dos equipamentos com o gerenciamento de risco poderá ser avaliado várias questões relacionadas com custos, risco envolvidos no tratamento a pacientes, custo de equipamento parado, imagem da instituição, receita perdida entre outras.
Todo este trabalho é voltado para atender uma demanda de solicitações ao setor de Engenharia Clinica que poderá auxiliar de uma maneira mais ampla a Gestão da Instituição.
INDICADORES MAIS UTILIZADOS
- Custo do programa de preventiva
- Custo com corretiva
- Disponibilidade de equipamentos
- Tempo médio entre falhas
- Tempo médio de reparo
- Manutenção preventiva realizada X planejada
- Manutenção corretiva
- Erro usuário
- Treinamento homem/hora
- Tempo de falha após preventiva
VANTAGENS DO GERENCIAMENTO DE RISCO
- Renegociação de contratos de manutenção
- Compra de equipamentos com cláusulas especificas em sua manutenção
- Segurança para ações jurídicas
- Redução de horas paradas do equipamento
- Levantamento real de necessidade de treinamento
- Materiais de estoque
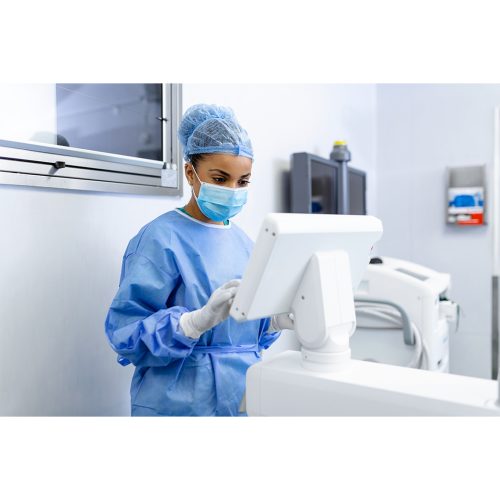
Evite a falha do seu Equipamento Médico-Hospitalar.
Agende uma consulta com o nosso engenheiro clínico para manutenção preventiva.
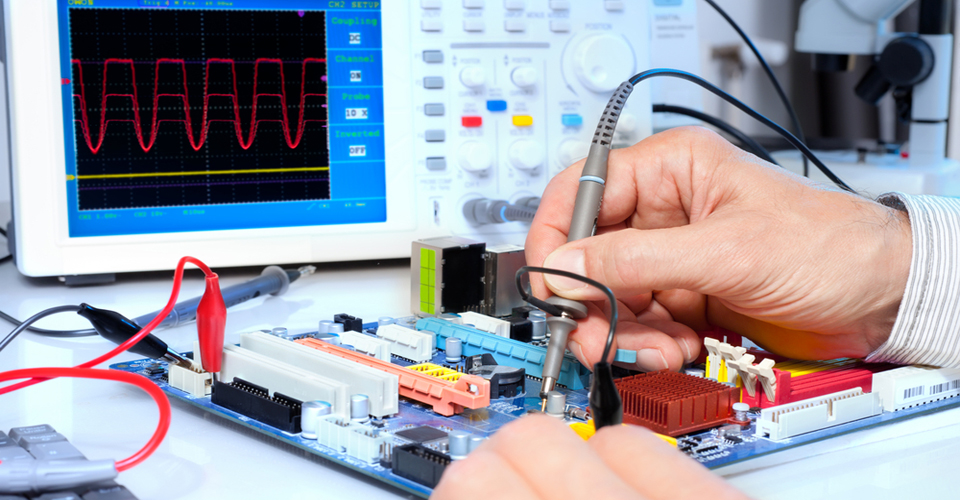